Authentication, Identification & Tracking Coatings
The Need for Authentication
There is a $512 billion global counterfeit epidemic according to the World Customs Organization. Everything from money to electronics, software, pharmaceuticals, clothing, watches, jewelry, automotive components, aircraft parts, documents, and all sorts of consumer products are frequently counterfeited.
Manufacturers:
- Spend tremendous amounts to develop and market their brand names, reputations and intellectual property, and they are forced to spend equally large sums of money and effort to protect their brands.
- Confront brand and product problems from not only counterfeiters, but all too often from their own suppliers or contractors.
- All too often are compelled to have extensive “Brand Protection” departments.
Consumers:
- Would like to know if their new set of golf clubs is the real deal and not some knock off made in Taiwan with an inferior alloy and weighting.
- Would like to know that the maintenance crew was able to verify that all spare parts installed on the plane are OEM approved parts before we board.
- Would like to know before we splurge on an extravagant watch, piece of name brand jewelry, sunglasses, or electronics that its not actually one of the cheap imitations you'd expect from a street vendor.
- Would appreciate if the price for the products we buy were not inflated by the expense manufacturers have to pay to protect their brands.
Metal Finishers:
- Want to be able to identify their product They receive crates of plated product from their customers with a complaint that the parts somehow do not meet specification. Perhaps the thickness, appearance, or corrosion resistance is not sufficient. And the customer expects the finisher to either strip and rework the parts, or sometimes simply to pay for the value of the part and coating. The problem is that these customers often use two or more finishers to coat their parts, and the shop receiving the rejected product may not know if the defective parts were actually coated in their shop or in the customer's inferior second source coater. So there is a value to finishers to have a way to readily tell if parts were or were not coated in their shop.
- Want to be able to offer their customers a new technology like this one that can be of unique value in product identification and tracking.
A new coating technology can now serve these important needs. There are four varieties of composite coatings that have been developed to provide authentication properties:
- Phosphorescent,
- Forensic Markers,
- Sound Activating Triggers, and
- Structured Micro Taggants.
Phosphorescence
|
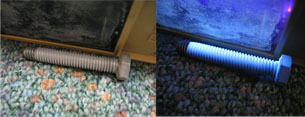 |
|
Photograph 1 – A bolt coated with one version of the Illumi-LayerTM coating with light emitting particles and photographed under normal (left) and ultraviolet light (right) to reveal the coating’s unique luminescence. |
This is the oldest variety of composite coating for authentication. Particles with light emitting properties have been incorporated within EN coatings. These novel coatings appear like normal EN under traditional lighting (sun, incandescent, fluorescent, etc.), but under an ultraviolet (UV) light, these coatings emit a distinct brightly colored glow. A person simply needs to shine a hand held, battery operated UV light on parts to display the light emission of a composite EN coating, and thereby confirm the authenticity of the parts. As there are a number of materials that fluoresce under UV light, it is possible to produce a variety of EN coatings that each give off a different color glow when a UV light source is shined on the coating. The technology of these light emitting coatings is further described in US Patents 5,514,479, 5,516,591, and 5,834,065.
This coating variety can also be used under a functional coating such as nickel or chrome to demonstrate wear to avoid damage to the part itself, and possibly prevent inferior or out of tolerance products from being produced from a worn part. A mold is a prime example. With a thin layer of a light emitting coating between the substrate and the functional coating an operator may then inspect the part periodically with a portable UV light, often while the part is still in use. Once colored light is observed, it is known that the functional coating has worn away. The part can then be recoated and reused before substrate damage to the part itself occurs and before inferior product is produced.
Forensic Markers
|
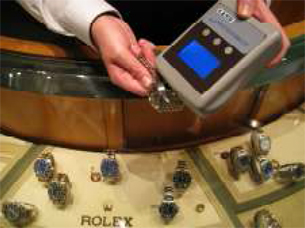 |
|
Photograph 2 – A detector displaying the presence of the TraceCoatTM coating which identifies a product as authentic. |
While the composite phosphorescent-EN coatings are a useful technology for many applications, other applications require an even greater need for covert authentication. This can be accomplished by the use of certain forensic markers which are a family of materials that have been developed using unique substances that each can be detected by an electronic meter. The test is non-invasive, instantaneous, and infinitely repeatable. These materials are chemically inert, safe and strong enough to persist in almost any conditions including an EN plating bath and heat treatment. Only small amounts of the ceramic based materials need to be co-deposited into the EN coating to make their properties evident to the electronic meter. Therefore the slight presence of the material in the coating is not readily visible and essentially does not affect the performance of the coating in other regards.
There are dozens of such materials, which can be used alone or in combination to create a unique marking or tracking system that can be embedded in almost any material or coating including EN. This makes possible many new opportunities for product management, manufacturing process and logistics control, inventory management, quality assurance, pollution control and authentication.
Each detectable material can be assigned a code number or a name. The electronic detector can be programmed to recognize each material and indicate the presence of one or multiple materials according to the pre-assigned code. For example, if a coating is produced with material “1”, the detector will report the presence of “1” in the coating. If the coating contains material “2”, the detector will report “2”. If the coating contains both “1” and “2”, the detector will report both “1” and “2”.
While this sounds simple, something we prefer in technology, the implication is significant. This ability of the detector to identify multiple materials and the existence of dozens of such proprietary materials means that hundreds of combinations can be employed within a coating, thereby allowing the finisher the opportunity to have coatings with embedded “codes” that indicate parts that were plated in their shop, an affiliated shop, and on specific days, months, years, or other time period.
This information is very useful to manufacturers both at the time of manufacture before product is shipped to their customers, as well as for tracking later on if any product is returned. This can be particularly valuable for a manufacturer in warranty situations, especially if the returned product can be proven to not be authentic.
Numerous security measures are even incorporated into the digital meter itself. Special circuitry has been installed so the device cannot be reverse engineered, and it will shut down and lock out if any unauthorized programming or inspections are made. Patent coverage further extends the ability to control this technology.
Sound Activating
|
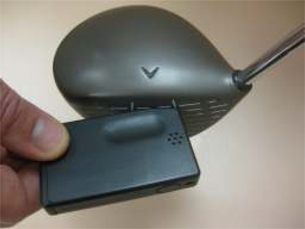 |
|
Photograph 3 – This extremely small detector makes a distinct sound when in contact with a specialty coating. |
As if the technology couldn’t get any more innovative, a further variety of authentication coating technology has been developed that actually allows the coating to activate a small detector to produce an audible report. This innovative technology is very similar to that using forensic markers since only a small quantity of a specialized materials need to be incorporated into the coating to trigger the response of the detector. While multiple frequencies or sounds are not yet available, the value of this variety of authenticating technology is its simplicity. The test is instantaneous and generates a clear pass/fail indication. This is a benefit to the finisher to verify the proper functionality of the coating, and to the end user to authenticate a coated product. And the detector is small and battery operated for the economy and convenience of the user.
Structured Micro Taggants
This variety of coating technology provides a fourth means of authentication of a product. Instead of visible light emission, electronic detection, an audible report, this variety is detected simply by inspection of the surface under magnification. A key to making this type of coating useful in authentication and product/brand protection is that the micro taggants are “structured”. They are structured in that they are made in a highly specialized way through a complex and proprietary process.
This process includes a number of variables that can be highly customized for the needs of individual applications. The manufacture of the taggants can impart a specific design on the taggants such as a logo, a code, numbers or symbols, etc. The size and materials of the taggants can also be altered. Even the concentration of the taggants in the coating can be deliberately adjusted according to the preference of manufacturer. Typically just one taggant in a 400x magnified field of view is sufficient for fast and reliable inspection and identification, but more taggants can be incorporated when desired.
The ability to customize the taggants in these ways means that the design of the taggants can be modified on a continual basis to thwart counterfeiters and/or incorporate product identification and tracking information literally right on the surface of the product within a hard and durable coating.
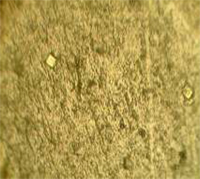 |
|
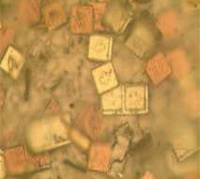 |
Photograph 4 – A 400x view of the surface of a coating incorporating structured micro taggants to permit authentication of a product simply by microscopic examination. |
|
Photograph 5 – A 1000x view of one example of structured micro taggants showing an intricate design able to be imparted into the taggant. |
For more information on these unique and exciting coatings for authentication, identification and tracking, please see the following links: